Precision molding is the latest technology in plastic injection molding. This type of plastic molding is the most sophisticated process of mold design on the market. It may be used for components that require an exceptionally precise form of plastic injection molding.[1]
About Precision Molding
Precision injection molding is a highly technical process requiring precision machines and molds. The process of precision molding is different from conventional injection molding techniques and is often used for developing precise plastic parts with complex geometries. These parts are often used as lightweight replacements for high-precision metal parts in industrial applications.
The precision of a part is dependent on the precision injection mold and its suitability for the engineering requirements. Many factors impact the precision injection mold, including:
- The precision of the parting surface
- The precision of the mold cavity size
- Accurate position of the cavity
- Choice of materials
- Number of cavities in the mold design
- Dimensional tolerance of general precision molds
- The thickness of the bottom plate, supporting plate, and cavity wall
- Runner size
- Design engineering
- The material of the precision mold
How Does Precision Molding Work?
Injection molding is a cost-effective way to replicate aspheric, spherical, and freeform surfaces and combine them with mounting features. There are three components to successful injection molding:
High Precision Mold
The mold used to manufacture polymer optics includes the cavity details, optical inserts, and housing to hold the cavities and inserts. Optical and mechanical features may be combined into one platform with polymer optics, which may lead to a mold with high complexity.
Molds are built to the negative of the final part, and the mechanical features of the part are drafted for easy removal once the molding process is complete. Most optical inserts are created from nonferrous alloys that are diamond turned for high accuracy.
Thermoplastics shrink as they cool. The shrinkage is roughly 0.5 to 0.6%, which must be considered when creating the mold.
Precision Injection Molding Machine
The optical injection molding machine, called a press, includes a fixed and a moving platen, a clamping unit, and an injection unit. The mold is placed on the press with one half mounted to the fixed platen, and the other half is mounted to the moving platen. Plastic pellets are melted, fed into the injection unit, and injected into the mold.
A clamp mechanism holds the two mold halves together during the injection process. As the polymer cools, it takes the shape of the cavity details and solidifies to create the final optic. Once cooled, the mold is opened and ejects the finished optic.
The Process
Injection molding uses complex variables and controls. Without a robust process, even the best mold will experience drift from tool wear, changes in ambient conditions, fluctuations in resin content, and more. This is why it’s essential to find an optics manufacturer with a high degree of skill in scientific molding techniques.
With the proper process, optical injection molding techniques can produce optical components with a high degree of repeatability and accuracy.
Applications for Precision Molding
Any application that calls for an optical component, such as components for machine vision, scanning, imaging, medical, or general illumination, may use a polymer optic.
You’ll often find polymer optics in supermarket barcode scanners, LIDAR, automobile sensors, and medical applications. They are also used in sophisticated laboratory equipment like spectrometers, cleanroom particle counters, document scanners, and more.
As applications grow, polymer optics finds its place in telecommunication products and microstructured surfaces such as diffractive optical elements and microlens arrays. Other examples include imaging systems for near-to-eye displays, PC peripherals, and consumer devices like DVD players and smartphones.
Many of these applications are the result of the advantages that polymer optics have over glass components. These advantages are a direct result of the materials and the injection molding process.
Precision Molding at Apollo Optical Systems
Several factors impact the quality of the finished optical component and the repeatability of the process. The design engineering process must include precise guidelines to reduce defects and ensure top quality. Apollo Optical Systems’ molding technology creates consistent, high-quality parts that meet or exceed industry standards for successful finished optical components. Contact us to discuss your custom optics project!
Sources:
[1] https://www.sciencedirect.com/science/article/abs/pii/S0141635922000319

About Dale Buralli
Dr. Dale Buralli has served as the Chief Scientist for Apollo Optical Systems since 2003. In this role, Dr. Buralli is responsible for the design and optical modeling of various optical systems. These systems include virtual or augmented reality, ophthalmic and other imaging or illumination systems. Additionally, he provides support for optical tooling of lens molds and prototypes, including the development of custom software for both production and metrology. Dr. Buralli got his Ph.D. in optics from the University of Rochester in 1991. Now he is an Adjunct Professor of Optics at the University of Rochester’s Institute of Optics.
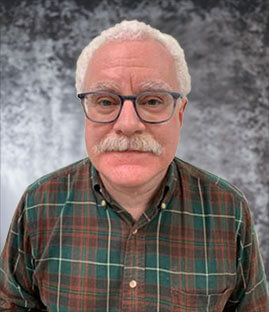