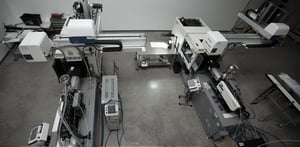
Glossary
Polymer Optics Terminology
Blanks & Pucks – raw or semi-finished material used as a starting point for creating a prototype. These materials are shaped, machined, or diamond turned to form the finished product. Blanks and pucks play essential roles in the prototyping phase, providing the foundation for creating and testing prototypes before moving into full-scale production.
Diffractive Optics – a type of optics based on elements with operating principles that rely on the diffraction of light. Diffraction is a consequence of the wave nature of light. Optical wavefronts interacting with apertures, structured surfaces, etc., produce effects that deviate from what might be expected from considering only straight-line light propagation. Diffractive optics, also known as diffractive optical elements (DOEs), are designed to achieve specific optical functions, often replacing, or complementing traditional refractive and reflective optical components like lenses, prisms, and mirrors.
Evaporative Coating – a coating process that involves the evaporation of materials to form a thin film stack on an optical surface. This coating technique enhances the performance and durability of polymer optics. A typical application is to reduce the optical reflectance of a surface within a certain wavelength range. Also, a reflective coating may be applied to a surface to turn what would otherwise be a transmissive surface into a mirror surface.
High-Precision Optical Components – components designed to offer a much higher level of accuracy and tolerance than typical optical components. In most cases, they need to function correctly within sub-micron-level tolerances to meet the demands of their application. These parts are manufactured using some of the most cutting-edge technologies available. In many cases, these include computer-controlled lathes and diamond-turning machines that process materials such as acrylic and other polymers, aluminum, brass, and nickel. The results are engineered products perfect for a wide range of precision applications.
Microlens Array – arrays of lenses usually arranged in a regular pattern on a substrate. A common function is to increase the light collection efficiency of charge-coupled device (CCD), CMOS, and other solid state sensor arrays. They serve to collect and focus light that would otherwise fall onto non-sensitive areas of the sensor array. In another application, microlens arrays are used in digital projectors to help focus light. Microlens arrays offer several benefits in optical applications, contributing to improved performance, miniaturization, and enhanced functionality.
Optical Assembly – a collection of optical components arranged to perform specific functions in an optical system. An optical assembly plays a crucial role in manipulating and directing light to achieve a desired outcome. Common components include lenses, mirrors, prisms, filters, apertures, and beam splitters.
Optical Diffusers – optical (or light) diffusers are devices that redistribute light into a desired pattern. They play an important role in various applications where achieving an even light distribution within a prescribed area is important. Optical diffusers are used to minimize glare, reduce hotspots, and enhance the overall quality of lighting.
Optical Metrology – the science and technology concerning measurements for components and systems that utilize light. Such measurements can either target the properties of light, light sources, optical images, or illumination distributions or the properties of objects used in optical systems such as dimensions, distances, and temperatures.
Optics – a branch of physics that studies the behavior and properties of light, including how it interacts with matter and how instruments can use light or detect it. Typically, optics refers to the behavior of ultraviolet, visible, and infrared light, but light is an electromagnetic wave, and other forms of electromagnetic radiation, such as microwaves, exhibit similar properties.
Optoelectronics – the study and application of light-emitting or light-detecting devices. It is widely considered a subdiscipline of photonics (q.v.). This fast-emerging technology field applies electronic devices to generating, detecting, and controlling light. It may be used for everything from military applications to telecommunications to medicine.
Photonics – a branch of optical science that involves the generation, detection, and manipulation of light for which the quantum nature of light particles (photons) is fundamental. Photonics is the science and engineering of photon emission, transmission, modulation, switching, amplification, signal processing, and sensing.
Polymer Injection Molding – Injection molding is a process in which a molten polymer is forced into a mold cavity under high pressure. The polymer is fed into the molding machine in pellet form, which is then softened, melted, and injected into the cavity to take the shape of the mold. The mold itself has a precise cooling system that allows controlled cooling and solidification of the polymer, which is then held in place until fully set. Injection molding is a production method that offers incredible control of manufactured parts and high accuracy, ensuring that identical parts can be mass-produced.
Polymer Optics – also called plastic optics, refers to the use of polymers in the design and manufacturing of optical components like lenses, mirrors, and prisms. These components are utilized in a variety of applications, such as imaging systems, lighting systems, sensors, and optical communication devices.
Precision Molding – plastic molding that is the most sophisticated process of mold design on the market. It may be used for components, like optical elements, that require an exceptionally precise form of plastic injection molding. Precision injection molding is a highly technical process requiring precision machines and molds. The process of precision molding is different from conventional injection molding techniques and is often used for developing precise plastic parts with complex geometries. Ideal applications for precision molding are any that call for an optical component, such as lenses or mirrors for machine vision, scanning, imaging, medical, or general illumination.
Refractive Optics – the branch of optics that deals with the manipulation and control of light using lenses and other optical elements based on the principles of refraction. Refraction is the phenomenon that occurs when light waves pass from one medium into another medium in which the light propagates with a different speed (i.e., the second medium has a different index of refraction), causing a change in the direction of the light. In refractive optics, lenses are commonly used to bend and focus light, enabling the formation of images and the control of light paths.
Single Point Diamond Turning – a manufacturing process that is used to produce low to moderate volumes of accurate and precise optics, typically for research and development or prototyping purposes. It uses mechanical machining of precision optical elements using machines equipped with diamond-tipped tool bits. The process used for single-point diamond turned optics may be applied to the manufacturing of high-quality aspheric optical elements from polymers, metals, crystals, and other materials.
Subassembly – a unit assembled separately but designed to be incorporated with other units into a larger manufactured product.
Substrate – a base material or surface on which subsequent layers, coatings, or processes are applied to create a final product. The choice of substrate depends on the specific characteristics required for the end product and the manufacturing processes involved. Substrates serve as a foundation or support for additional materials or functionalities. In optical systems, the materials used for the individual optical elements (e.g., lenses) form the substrates onto which coatings are applied.
UV bonding – also known as ultraviolet (UV) light bonding or UV curing bonding, a process used in manufacturing and various industries for joining or bonding materials. This technique relies on the use of a specially formulated adhesive or resin that cures or hardens when exposed to UV light.
Witness Samples – small representative pieces or specimens of material that are created for testing or inspection purposes. These samples are considered “witnesses” because they are used to observe and evaluate the properties and characteristics of the material, especially in terms of optical performance. A common use of a witness sample is during the deposition of an evaporative coating. The witness samples can be used to measure the transmittance or reflectance of the coated surface to ensure that it meets specifications.