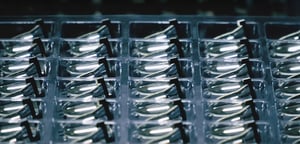
Injection Molding
Explore the Versatility of Injection Molding in Polymer Part Manufacturing
Injection molding is a manufacturing technology used to mass produce identical polymer parts.[1] The polymer granules are melted and injected under pressure into a mold, which then cools and solidifies.
Nearly every plastic part you encounter was manufactured with injection molding, including some electronics components, kitchen appliances, and car parts. This manufacturing method is popular because of its low cost for high-volume production, high repeatability, and excellent design flexibility.
How Injection Molding Works
Injection molding is a popular manufacturing method for polymer parts. It has a wide range of uses, including consumer electronics, packaging, toys, and miniature, complex industrial uses like medical technology and automotive manufacturing.
Here are some common examples of injection-molded products:
- LEGO bricks
- Bottle caps
- Model airplanes
- Car parts like bumpers, dashboards, and interior pieces
- Consumer electronics
- Sterilizable and biocompatible materials for medical devices
- Diagnostic test kits
- Surgical prep products
- Window roller assembly
- Conveyor system components
- Food and beverage containers
- Beverage filtering components
The Manufacturing, Design Guide & Use
An injection molding machine consists of three parts:
- The injection unit
- The mold
- The clamping/ejector unit
The injection unit is used to melt the raw polymer and guide it into the mold, consisting of the hopper, barrel, and reciprocating screw.
The injection molding process is as follows:[2]
The polymer granules are dried and placed in a hopper, where they are mixed with reinforcing additives or pigments.
The polymer granules are fed into the barrel, where they are heated, mixed, and shifted toward the mold by the screw. Both the screw and barrel are optimized to create pressure buildup and melt the polymer material.
The ram moves forward, and the melted polymer is injected into the mold with the runner system. As it cools, it solidifies and takes on the shape of the surrounding mold.
When the process is finished, the mold opens, and the ejector pins eject the solid piece.
The process is repeated for each unit.
As a whole, the injection molding process takes around 30 to 90 seconds to complete a full cycle for each individual unit. Injection-molded parts are typically ready to use immediately and require no post-processing.
The mold for injection molding is similar to a photo negative. The surface texture and geometry are reversed and transferred onto the injection-molded unit. A high level of expertise is required to design and manufacture a high-quality mold that can accurately produce hundreds of thousands of components.
Molds are typically machined out of aluminum or steel with a CNC. They may have additional features beyond the negative of the part, such as the runner system or internal water cooling components.
Why Choose Us for Custom Injection Molding?
Several factors may affect the final unit’s quality and the process’s repeatability. A designer must follow precise design guidelines to reduce defects and ensure quality.
Apollo Optical System’s molding technology ensures consistent, high-quality parts that meet or exceed all industry standards. We work closely with our customers to ensure mutual success in the finished optical design.
We can design and create a variety of optical components in-house, including anti-reflective and evaporative coatings, custom optical diffusers, diffractive surfaces, and spherical, aspheric, and Fresnel surfaces. Contact us today to discuss your custom optics project!
Sources:
[1] https://spie.org/samples/FG37.pdf
[2] https://wp.optics.arizona.edu/optomech/wp-content/uploads/sites/53/2016/10/Plastic-Optics.pdf
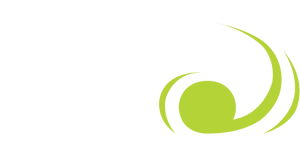